About the Project
The new 14-story 430,000 SF WMATA Virginia Headquarters Building is one of three new headquarters buildings to support WMATA operations. The $252 million Class A office building accommodates over 1,400 employees and includes three parking levels, a 40,000 SF operation command center, a prominent main lobby entrance and building amenities. This building serves as a technology hub for WMATA and is home to critical support spaces, including cybersecurity operations, bus and rail video teams, communications and administrative support. Building amenities include a fitness center, green roof, amenity penthouse suite and an innovation lab. This multipurpose lab space is available for public use, such as school groups, to learn about current transit and the history of transit.
The structure is constructed of cast-in-place concrete and includes precast cladding. The building features a window wall facing with intermittent precast spandrels on levels 5-14. Critical operational components include a 40,000 SF operation command center for rail, bus and security operations, which features 18” raised access flooring. Critical support spaces feature three-foot raised access flooring and was turned over six months prior to the completion of the building for loading equipment and data transfer.
“WMATA appreciates Hensel Phelps’ successful coordination, management and execution of the project to create a new and improved workplace headquarters for WMATA. The Hensel Phelps project team adopted a highly collaborative approach to managing the project, ensuring open and transparent communication with WMATA throughout project duration.”
NIA RUBIN, DIRECTOR OF REAL ESTATE DEVELOPMENT AT WMATA
Challenge
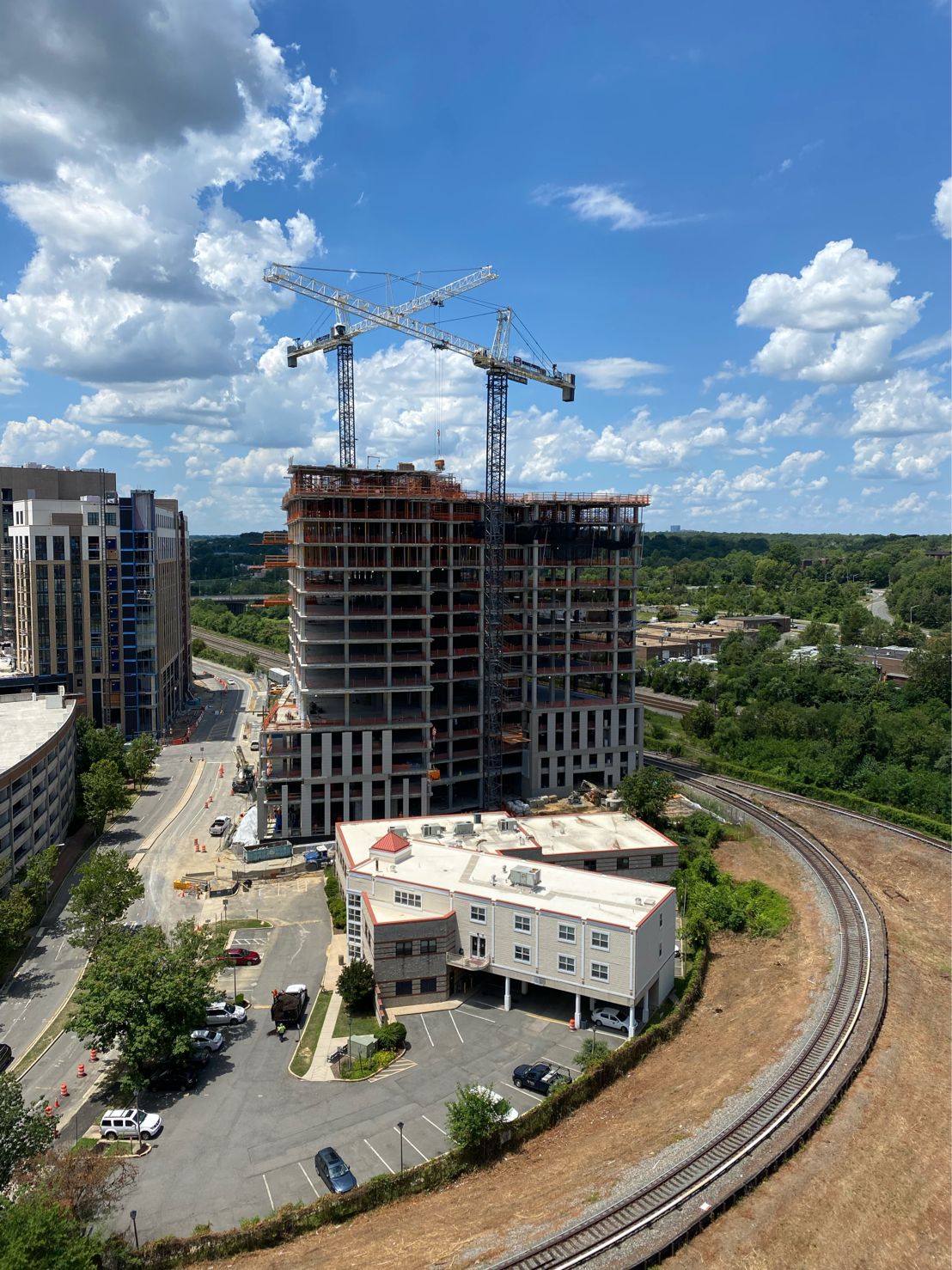
Erection of Skin Adjacent to Active Tracks
The WMATA Virginia Headquarters building is located directly adjacent to a WMATA rail line and associated tunnel. All work along the WMATA track right-of-way (ROW) is controlled and monitored by the Joint Development for Adjacent Construction group (JDAC), which oversees all construction projects within the stated Zone of Influence (ZOI), about 25′ of the WMATA ROW. All construction activities that could potentially cause risk to the WMATA rail, including the erection of the building skin, required review and approval by JDAC.
Solution
Mitigating Potential Risks
Throughout the precast and glazing on the project, the JDAC raised concerns about potential incidents that could foul the tracks and endanger the rail and/or pedestrians. The initial review of the erection plans dictated that erection on the north side of the building (within 25 feet of the tracks) could only occur during non-revenue train hours. Through multiple meetings and coordination with WMATA and JDAC, the project team was able to limit the erection restrictions on the north side of the building to the area directly over the open tunnel portal on the west half of the building. Restrictions largely consisted of erecting the northwest portion of the building only during non-revenue hours, which proved to vary widely based on multiple factors. They were originally set for 1:00 AM and 3:30 AM. A WMATA attendant with a radio was always present on-site during erection in case of emergency or incident requiring the shutdown of trains.
Schedule Coordination Through Sequencing
The restrictions placed on the erection of the skin system on the north side of the building required detailed coordination and severely limited/dictated the sequence of erection. The need to erect the building with tower cranes on the east and west sides of the building, coupled with the restrictions on the northwest side, caused the building erection to fall behind on either side rather than bringing the skin system up floor by floor. The milestones of the project relied heavily on coordination around the track rights times and hours granted by WMATA and JDAC. The track rights are the time allowed for working within this restricted zone, and changed weekly and varied night to night, drastically affecting the dry-in milestones for the project, including the data center located on the north side of level 5, and causing difficulty in accurately scheduling the work and completion milestones. To keep the schedule productive, Hensel Phelps kept areas of the building outside of the WMATA ZOI available for access to work until track rights were granted. To help accommodate this, the project team rented a lot adjacent to the jobsite to store 15 to 20 precast trailers and assigned a truck driver to transport them into and out of the jobsite, allowing for flexibility in the timeline needed for the erection of the building. If track rights were not granted—or were granted earlier or later than expected, Hensel Phelps could quickly adjust by preparing the appropriate panels for installation, minimizing crew downtime.
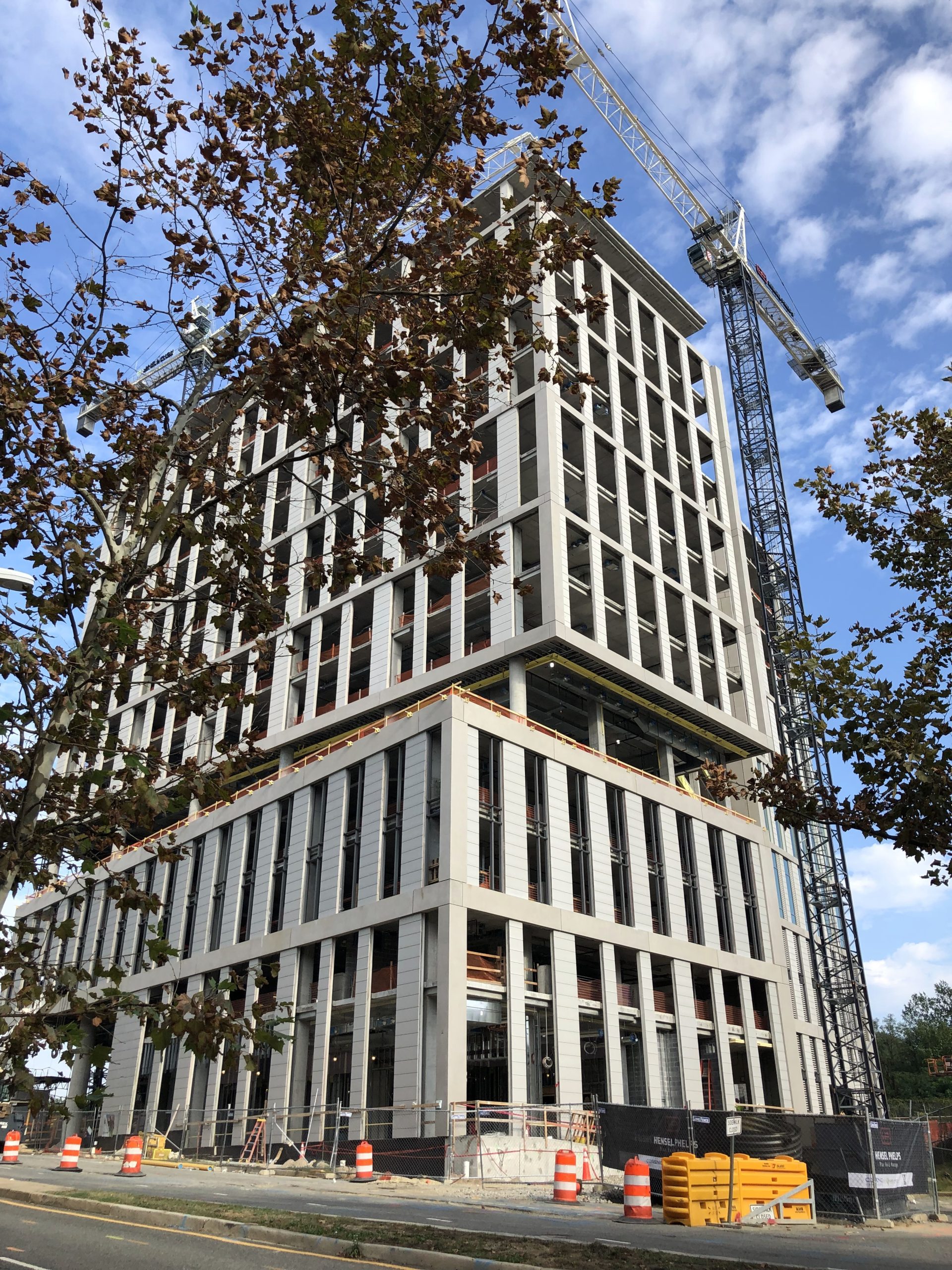
Results
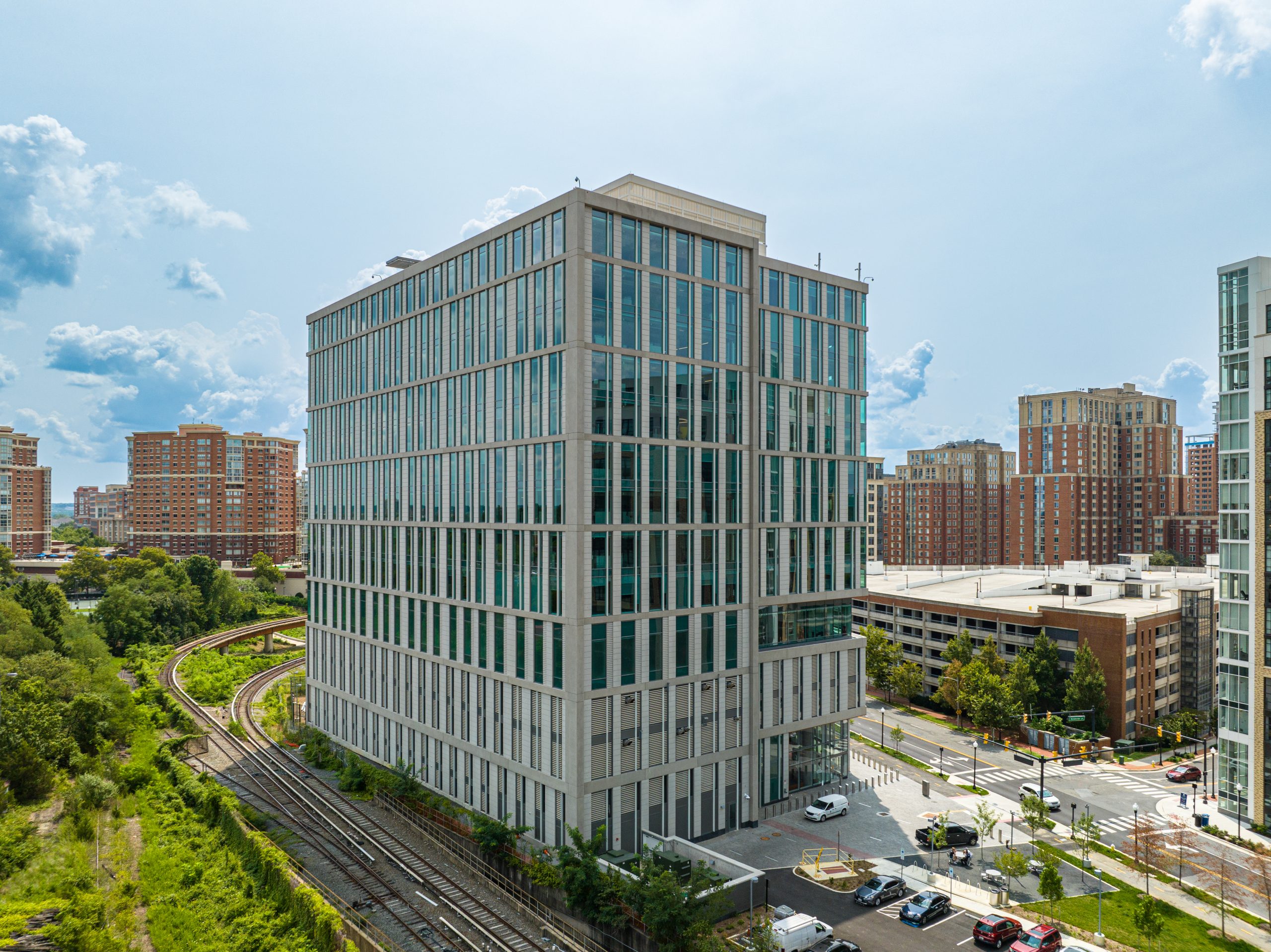
Lessons Learned
While Hensel Phelps successfully erected the skin system on the northwest side of the building, several lessons learned emerged from this process. For example, when planning a project or scope of work with the WMATA ZOI for rail lines, Hensel Phelps should bring the JDAC and WMATA groups on board early in the planning process to fully understand the restrictions imposed in the scope of work to adjust the plan and schedule for the project. Contingency plans for varying hours of track rights are also imperative to stay productive.
Awards
2024
Associated Builders and Contractors (ABC) Excellence in Construction (EIC) Eagle Award for Mega-Project over $250 million